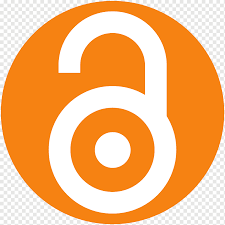
FAILURE THRESHOLD DETERMINATION OF ROLLING ELEMENT BEARINGS: VIBRATION FLUCTUATION ANALYSIS AND FAILURE MODES INVESTIGATION
Abstract
Rolling element bearings are critical components in many industrial applications, and their failure can lead to significant downtime and maintenance costs. Therefore, predicting the remaining useful life of bearings is essential for effective maintenance scheduling and avoiding unplanned downtime. In this study, vibration fluctuation analysis and failure modes investigation were employed to determine the failure threshold of rolling element bearings. Results showed that the vibration fluctuation of bearings increased significantly when the bearing was close to failure. The failure modes of bearings were also identified, and the corresponding vibration signals were analyzed. Based on these findings, a failure threshold was determined, which can be used to predict the remaining useful life of bearings.
Keywords
Rolling element bearings, vibration fluctuation analysis, failure modes investigation
References
Mahamad, A.K.; Saon, S.; Hiyama, T. Predicting remaining useful life of rotating machinery based artificial neural network. Comput. Math. Appl. 2010, 60, 1078–1087. [Google Scholar] [CrossRef][Green Version]
ISO. Standard ISO 13381-1. Condition Monitoring and Diagnostics of Machines—Prognostics—Part 1: General Guidelines; ISO: Geneva, Switzerland, 2015. [Google Scholar]
ISO. Standard ISO 10816-3. Mechanical Vibration—Evaluation of Machine Vibration by Measurements on Non-Rotating Parts—Part 3: Industrial Machines with Normal Power above 15 kW and Nominal Speeds between 120 r/min and 15000 r/min; ISO: Geneva, Switzerland, 2009. [Google Scholar]
Elasha, F.; Shanbr, S.; Li, X.; Mba, D. Prognosis of a wind turbine gearbox bearing using supervised machine learning. Sensors 2019, 19, 3092. [Google Scholar] [CrossRef] [PubMed][Green Version]
Wang, D.; Tsui, K.L. Two novel mixed effects models for prognostics of rolling element bearings. Mech. Syst. Signal Process. 2018, 99, 1–13. [Google Scholar] [CrossRef]
Wang, Y.; Peng, Y.; Zi, Y.; Jin, X.; Tsui, K.L. A Two-Stage Data-Driven-Based Prognostic Approach for Bearing Degradation Problem. IEEE Trans. Ind. Inform. 2016, 12, 924–932. [Google Scholar] [CrossRef]
Lim, C.K.R.; Mba, D. Switching Kalman filter for failure prognostic. Mech. Syst. Signal Process. 2015, 52, 426–435. [Google Scholar] [CrossRef]
Bastami, A.R.; Aasi, A.; Arghand, H.A. Estimation of remaining useful life of rolling element bearings using wavelet packet decomposition and artificial neural network. IJSTE 2019, 43, 233–245. [Google Scholar] [CrossRef]
Nectoux, P.; Gouriveau, R.; Medjaher, K.; Ramasso, E.; Chebel-Morello, B.; Zerhouni, N.; Varnier, C. PRONOSTIA: An experimental platform for bearings accelerated degradation tests. In Proceedings of the IEEE International Conference on Prognostics and Health Management, Denver, CO, USA, 18–21 June 2012; Available online: https://hal.archives-ouvertes.fr/hal-00719503 (accessed on 20 July 2012).
Behzad, M.; Arghand, H.A.; Bastami, A.R. Remaining useful life prediction of ball-bearings based on high-frequency vibration features. Proc. Inst. Mech. Eng. Part C J. Mech. Eng. Sci. 2018, 232, 3224–3234. [Google Scholar] [CrossRef]
Behzad, M.; Arghand, H.A.; Bastami, A.R. Rolling Element Bearings Prognostics Using High-Frequency Spectrum of Offline Vibration Condition Monitoring Data. In Proceedings of the Condition Monitoring and Diagnostic Engineering Management, Rustenburg, South Africa, 2–5 July 2018. [Google Scholar]
Li, N.; Lei, Y.; Lin, J.; Ding, S.X. An improved exponential model for predicting remaining useful life of rolling element bearings. IEEE Trans. Ind. Electron. 2015, 62, 7762–7773. [Google Scholar] [CrossRef]
Wang, P.; Coit, D.W. Reliability and degradation modeling with random or uncertain failure threshold. In Proceedings of the 2007 Annual Reliability and Maintainability Symposium, Orlando, FL, USA, 22–25 January 2007. [Google Scholar] [CrossRef]
Nystad, B.H.; Gola, G.; Hulsund, J.E. Lifetime models for remaining useful life estimation with randomly distributed failure thresholds. In Proceedings of the First European Conference of the Prognostics and Health Management Society, 2012; Available online: https://www.phmsociety.org/node/788 (accessed on 30 May 2012).
Yu, T.; Fuh, C.D. Estimation of Time to Hard Failure Distributions Using a Three-Stage Method. IEEE Trans. Reliab. 2010, 59, 405–412. [Google Scholar] [CrossRef]
Qiu, H.; Lee, J.; Lin, J.; Yu, G. Wavelet Filter-based Weak Signature Detection Method and its Application on Roller Bearing Prognostics. J. Sound Vib. 2006, 289, 1066–1090. [Google Scholar] [CrossRef]
Tobon-Mejia, D.A.; Medjaher, K.; Zerhouni, N.; Tripot, G. A Data-Driven Failure Prognostics Method Based on Mixture of Gaussians Hidden Markov Models. IEEE Trans. Reliab. 2012, 61, 491–503. [Google Scholar] [CrossRef][Green Version]
Cui, L.; Wang, X.; Xu, Y.; Jiang, H.; Zhou, J. A novel switching unscented Kalman filter method for remaining useful life prediction of rolling bearing. Measurement 2019, 135, 678–684. [Google Scholar] [CrossRef]
Behzad, M.; Arghand, H.A.; Bastami, A.R.; Zuo, M.J. Prognostics of rolling element bearings with the combination of Paris law and reliability method. In Proceedings of the 2017 Prognostics and System Health Management Conference, Harbin, China, 9–12 July 2017. [Google Scholar] [CrossRef]